Application
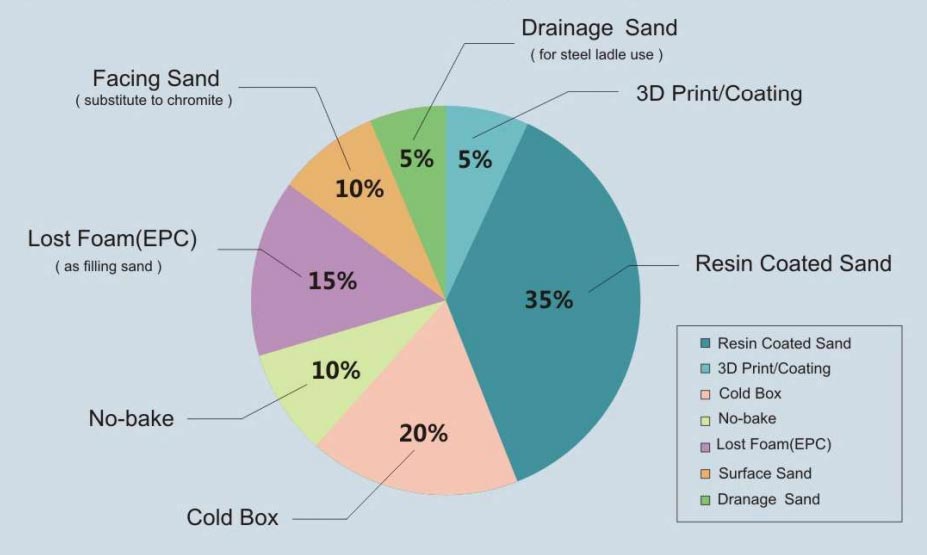
- 1.Furane Bonded Sand, Molding and Core Making
For Furan bonded Ceramic Foundry Sand, its hardening rate is much higher than silica sand. And when adding the same amount of resin, the strength is highly improved especially the tensile strength after placed for 24 hours, which is over 50% higher than that of silica sand. I has been proved that the use of Ceramic Foundry Sand can not only reduce the amount of resin, save costs, improve production efficiency, but also greatly reduce the casting defects such as porosity
- 2.Cold-box Process
The silica sand cores of some engine parts such as the cylinder block, cylinder head, the intake and exhaust manifold, etc., which have complex shapes and small cross sections. It is not easy to be filled by blowing and is easy to be fractured, also cause some defects in the castings such as veins, sand burn-on or metal penetration, porosity, etc. When using the Ceramic Foundry Sand or to mix with silica sand together, the content of the resin can be reduced by 20-30% and the above defects have been significantly eliminated
- 3.Resin caxted Sand Molding
Taking advantages of the Ceramic Foundry Sand, people can make high quality resin coated sand which has exceptional properties such as high temperature resistance, low expansion, easy to shakeout, high strength, and less gas evolution. The shell process of the Ceramic Foundry Sand is of high production efficiency, the casting dimensional accuracy and the castings finish are exceptional. The used sand is easy to recycle which greatly reduces the emission of solid wastes. The environmental benefits of this process are also remarkable
- 4.Alkaline-phenolic Resin Molding and Core Making
The pouring temperature of cast steel is rather high, the use of Ceramic Foundry Sand can fully take the advantages of the alkaline phenolic resin. The sand consumption of casting can be reduced to 30-50 kg per ton, the binder consumption is reduced by 30-50%. With the improvement of casting surface quality, the amount of sand shakeout and casting cleaning work can be reduced more than 60%. It also reduces the emission of waste gas, sand and dust, improves the work environment, prevents silicosis and achieves the goal of green production
- 5.Sodium -silicate Bonded sand
In CO2 silicate process, 3-5% water-glass is added into the Ceramic Foundry Sand then stirred. The mixture if firstly filled in the locations with heavy sections where easy to cause metal penetration, then the rest parts are filled with silica sand. The moulds are coated after hardening. The casting is easy to clean and the surface perfect. It can play a role of anti-penetration sand
- 6.Lost Foam Pracess and V-process
People use Ceramic Foundry Sand as backing sand for lost foam process and V-process. The rate of qualified products increases remarkably. The total cost decreases, the sand consumption of castings is only 1-2 kg per ton. And, the working environment is obviously improved because of its round shape, good flow-ability, lower dust, etc.
- 7.3D Printing
Ceramic Foundry Sand, a developed special artificial sand especially to meet the demand for 3D printing sand molds and cores, has brilliant appearance and good spherical shape. Those 3D printing company who uses this kind of sand, will take the advantages, such as reduced resin (binder) consumption, high strength, fast curing, excellent sand mold (core or shell) surface quality and customized particle size distribution.
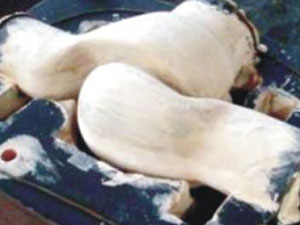
Mold and Cores (alpha set)
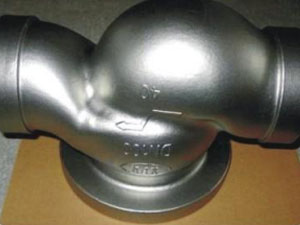
Valve Casting(low alloy steel)
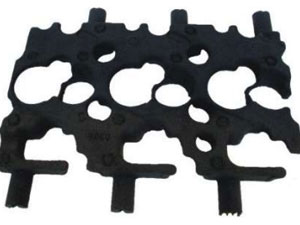
Cylinder Head Core(hot box)
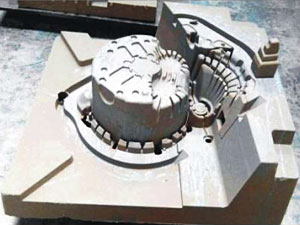
Cores/molds By 3D Printing
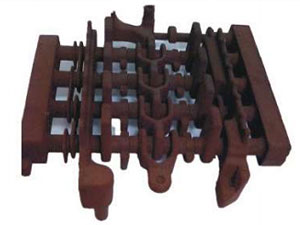
Core of Complicated Water Channel(hot box)
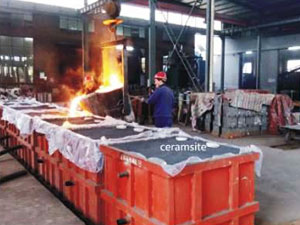
Pouring(EPC process)
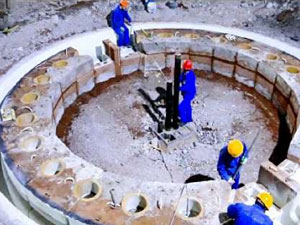
Ceramic Sand used as Facing Sand by Sodium Silicate Process
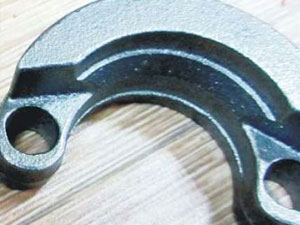
Stainless Steel Component Made By Shell Method
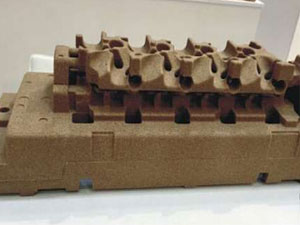